
Les supports de moteur sont la partie structurelle de la salle des machines qui soutiennent le moteur. Il ne faut pas les confondre avec les pieds de moteur. Sur les trois photos ci-dessous, les supports de moteur sont clairement visibles sur la première photo, tandis que la troisième photo montre un pied de moteur.
Pour la plupart des bateaux, c’est les supports de moteur qui absorbent la poussée de l’hélice est le transfère à la coque, faisant avancer le bateau. Comme le moteur peut changer de direction, comme lorsqu’on manœuvre dans un espace restreint, les supports du moteur doivent être structurellement solides, suffisamment pour résister à plusieurs newtons (livres) de force dû aux changements de poussée.
J’ai trouvé quatre archetypes de supports à moteurs. Le premier est plus une catégorie et se réfère à un moule en fibre de verre fixé à la coque. C’est du sur mesure et je n’ai pas recherché davantage. Les trois autres modèles commencent par des supports en bois collés à la coque. Les différences entre chacun proviennent de la façon dont le moteur est fixé aux supports.
Dans le premier modèle, le moteur est boulonné à travers le bois (première photo ci-dessous). Dans le deuxième modèle, le moteur est boulonné à travers un coin en acier, lui-même boulonné à travers le côté des supports en bois (deuxième photo ci-dessous). Dans le troisième modèle, le moteur est vissé directement dans les supports à l’aide de vis à bois (troisième photo).



Le boulonnage traversant le bois est une meilleure approche parce que c’est l’ensemble du boulon maintient le moteur en place plutôt que les filets de vis. Il y a moins de risques que le moteur se détache des supports sous l’effet des vibrations. Par rapport à la conception de la barre d’acier à 90°, la première conception est structurellement la plus solide : il y a un nombre minimum de pièces et le moteur repose sur les supports, ce qui réduit les forces latérales (et donc la torsion). Cependant, la première conception rend le remplacement d’un boulon plus difficile si ce dernier casse.
Avec le second modèle, les boulons traversant étant placés de part et d’autre des supports du moteur, ils peuvent être remplacés facilement. De même, les barres d’acier à 90° peuvent être remplacées si elles sont endommagées. Le second modèle est donc plus facile à entretenir. Toutefois, comme le moteur se trouve entre les supports, ces derniers doivent être plus petits pour tenir dans le compartiment moteur. De plus, le moteur génère une force latérale sur les supports, ce qui augmente la contrainte de torsion sur la fibre de verre. S’il y a rupture de la liaison mécanique en torsion, les supports doivent être entièrement reconstruits.
La première solution est la plus difficile à faire, car la position des pieds du moteur doit être connue avec précision avant l’installation. Il peut s’agir d’une bonne solution de remplacement si l’on utilise le même moteur et si l’on sait où il se trouve par rapport à l’arbre de transmission. Partir de zéro avec un nouveau groupe motopropulseur reviendrait toutefois à s’appuyer sur des mesures théoriques pour sa construction, ce qui constitue un risque.
Les deuxième et troisième conceptions permettent de percer les trous une fois que le moteur est en place. Ils sont donc plus faciles à mettre en œuvre. Cependant, la deuxième conception nécessite des supports moins larges et donc plus de précision quant à l’endroit où ils doivent être collés sur la coque.
En revanche, la troisième conception permet des supports plus larges et donc une plus grande marge de manœuvre latérale pour l’alignement du moteur. Il supporte en outre la charge du moteur directement par le haut. Ainsi, le seul point faible de la troisième conception, par rapport à la première, est l’utilisation de vis à bois. Il a également l’avantage d’être plus facile à mettre en œuvre. Comme il n’y avait pas de moteur sur Jean-du-Sud avant l’installation, j’ai utilisé le troisième modèle.
Plans et conception
Sur la base d’analyses antérieures, je savais que le moteur est à un angle de 11° vers le bas. J’ai conçu les supports du moteur à l’aide d’un rapporteur laser de manière à ce qu’ils correspondent à cette mesure, en pointant vers le bas le trou du tube d’étambot (photo au début du texte).
J’ai mesuré la hauteur des supports au centre des deux pieds du moteur. out cela pour dire que j’ai pris plusieurs mesures pour m’assurer que le plan des supports auraient une erreur qui serait suffisamment petite pour qu’elle puisse être corrigée la marge d’ajustement des vis sur chaque pied de moteur. La conception des supports de moteur est illustrée dans les photos ci-dessous. La première image montre la vue d’ensemble des supports. L’autre image divise le dessin en morceaux de 1 5/8″ x 3 1/2″ (2″ x 4″ laminés).




J’ai choisi du chêne blanc pour les supports de moteur. L’idée est de choisir un bois dur. Les pièces ont été vissées ensemble et collées avec de la colle à bois, en faisant très attention de ne pas placer de vis à l’endroit où les pieds du moteur étaient prévus. Le résultat est illustré dans les deux photos ci-dessous.
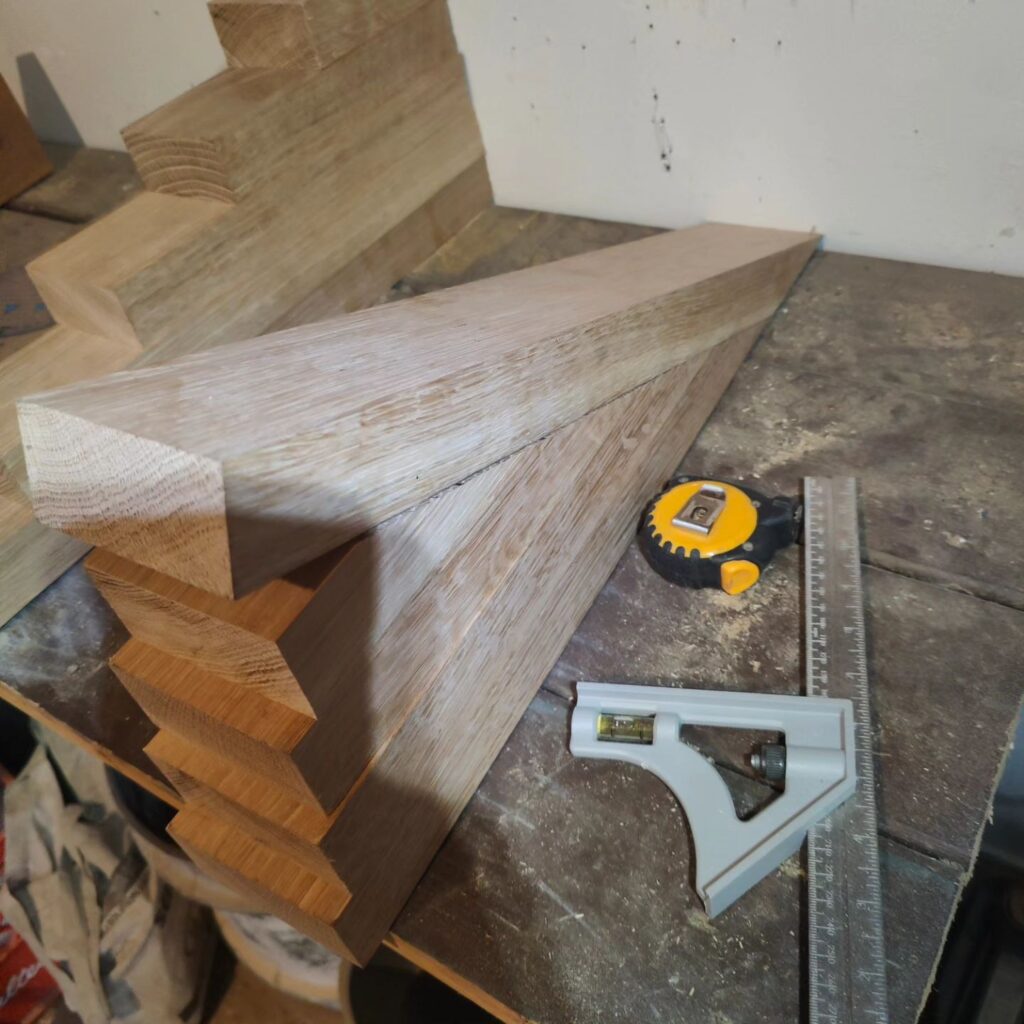

L’application de la fibre de verre sur les supports s’est faite en deux parties. La première partie consiste à remplir l’espace sous les supports et la coque. J’ai appliqué de l’époxy épaissi (beurre de pinottes) sur les coins des supports, à la fois sous et sur les côtés, afin d’avoir une première bonne couche de résine d’époxy. Ensuite, j’ai utilisé du mastic de résine polyester pour remplir la plus grande partie de ce qui se trouve sous les supports. J’ai ensuite terminé avec de la résine d’époxy épaissie pour la dernière couche de résine. Ainsi, le dessous des supports est un « sandwich » composé de deux faces de résine d’époxy épaissie et d’un centre de mastic polyester. L’ensemble a été poncé pour offrir une surface lisse à laquelle la fibre de verre fut posée.
La deuxième partie consiste à poser la fibre de verre. Le dessin des pièces en fibre de verre est présenté dans l’image ci-dessous. Il suit l’idée exposée dans la vidéo de BoatWorks Today (« How to Fiberglass Over Plywood », voir la section sur la fibre de verre), c’est-à-dire trois pièces de fibre de verre qui se chevauchent sur les côtés plans des supports : la pièce supérieure, la pièce extérieure et la pièce intérieure. Les pièces intérieures et extérieures sont bien sûr beaucoup plus larges que les supports eux-mêmes, ce qui augmente la liaison avec la coque grâce à une plus grande surface de contact.

Une fois les surfaces sablées, nettoyées à l’acétone et les morceaux de fibre de verre coupés aux bonnes dimensions, les supports ont été collés à la fibre de verre en moins de 30 minutes. J’ai utilisé trois couches de mat de fibre de verre de 10 oz.

Si j’avais su…
Si je devais refaire les supports avec les mêmes informations sur la position du moteur, je changerais probablement trois choses. Premièrement, au lieu d’assembler le chêne avant de l’installer, je boulonnerais la pièce inférieure de manière à ce que les boulons figent dans la résine d’époxy épaissie.
Deuxièmement, j’utiliserais un moule pour verser toute la résine d’époxy épaissie sous les supports en une seule application. Ensuite, j’assemblerais les pièces restantes des supports de moteur à l’aide de colle et de vis. Cette approche augmenterait la force de la liaison entre la coque et les supports.
Troisièmement, j’augmenterais la hauteur des supports au niveau des pieds de moteur avant d’environ 6 millimètres (un quart de pouce) afin d’obtenir un meilleur alignement des supports. Cette augmentation est bien à l’intérieur de la marge d’erreur des pieds du moteur, mais cela aurait été mieux que l’insertion de plaques d’acier ajoutées lors de l’alignement.
En savoir plus
Vous pouvez en apprendre davantage en lisant la section « entretien » de ce site. Il contient d’autres techniques de rénovation et de construction de bateau.
Références
CruisersForum.com (2021). Fiberglass reinforcements to restore an odd engine bed structure, récupéré en ligne en Octobre 2023 à cette adresse.